In 2020, the World Economic Forum stated that a majority of the largest manufacturing organizations were stuck in pilot purgatory. When companies can’t move their most transformative ideas out of the pilot phase, they never realize the value of the pilot. Four years later, this is still the case. The aspirations and full benefits of Industry 4.0 are not being realized for at least 70% of manufacturers and their respective supply chains. Our own research at ISG has shown this number may be closer to 80%.
What are the manufacturers that are successfully applying and gaining value with Industry 4.0 doing? These companies are referred to as Lighthouse Factories – and they are attributing their success to two things. One is their ability to leverage digital implementations and technological advancements. And the second is their ability to manage a truly holistic transformation that incorporates humans, data and processes while keeping their brand identity authentic.
As of April 2024, the majority of these Lighthouse Factories are found in Asia and, more specifically, China. To date, there are 22 different maturity and capability standards for Industry 4.0, with no single one being widely accepted. The investment required for a manufacturer to become a Lighthouse Factory is in the billions of dollars and potentially years of time. The market is full of service providers and technology players trying to sell piecemeal solutions; the way forward can be confusing.
One key problem the manufacturing industry needs to solve is the divide between information technology (IT) and operational technology (OT). Companies need to finally accomplish the long-awaited IT-OT convergence. This concept originated in 2011, focusing on the cognitive shop floor and smart production enabled by:
Flexibility of mechanical procedures
Feedback loop for true closed-loop manufacturing
Digital twin capabilities
Smart and sustainable operations and production
This is not a pipedream, as successful examples exist. Most if not all OEMs are developing products using this approach. BMW and Mercedes factories in Regensburg and Sindelfingen are recognized Lighthouses. In BMW’s case, the factory was aided by the close alignment of its strategic plan to improve operating performance with its Strategy Number One program. At the Mercedes factory, the modern working practices include production staff in the design. This is a form of industrial democracy seen at the long-time manufacturing leader Semco, among other places.
Manufacturers will be left behind without the principles of IT-OT convergence. Without it, OEMs will face serious impediments that will result in slower production and the inability to be agile for new features and services.Please fill out this form to continue.
Why Has Industry 4.0 Not Worked So Far?
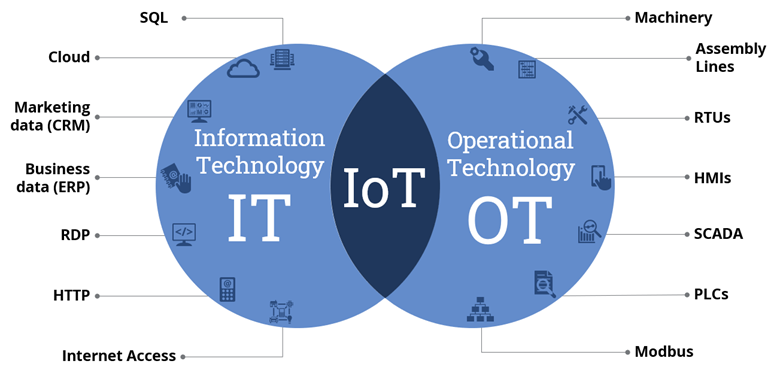
Figure 1: Information Technology (IT) & Operational Technology (OT) Convergence: How Does It Benefit Digital Manufacturing
Source: Tanand Technology
Traditional manufacturers arose from the Second Industrial Revolution and gained operational benefits from digital improvements occurring in the digital revolution. Those digital improvements extended to the non-core manufacturing or product parts of the business, such as the corporate and enterprise functions of Finance and HR. As these implementations were logically separated by “core product” and utility or “support,” they became systems that served as separate islands, each with its own specific purpose.
OT is not architected like IT. OT is integral to industrial operations and production processes with specific demands related to remote manufacturing plants in a supply chain. IT’s premise is about the exchange of information. OT has traditionally had minimal communication across systems. Operational concepts such as open source have been foreign to OT, with most being protected by proprietary software and communication protocols. The machines and software relevant to OT were intended to be stable and to last for decades. In some extreme examples, there are OT systems that are half a century old.
IT, on the other hand, sees faster obsolescence, with user experience as a pivotal consideration. In the past, software and technology vendors rarely overlapped across IT and OT. Development approaches also differed with IT pushing for faster iterations and continuous feedback for users through agile development. Such a concept would have detrimental impacts in the product world, with safety and quality being keys to success. This is starting to occur in some cases like SpaceX, but safety and quality in production lines typically prohibit such iterative work. Over time a divergence between IT systems and OT systems became wider and more pronounced.
Industry 4.0 works on the premise of interoperability and scale across the entire value chain, including both IT and OT to enable smart industrial practices. It has simply not been possible with these differences.
Figure 2: IT-OT Convergence Is a Requirement for Smart Manufacturing
Source: LinkedIn
What Needs to Converge?
New capabilities and technical advances in automation brought the first glimpse of opportunity to share data seamlessly between IT and OT. Sensors in IoT devices began to build the bridge toward this convergence. Edge computing started to erode the strict separation between OT and IT.
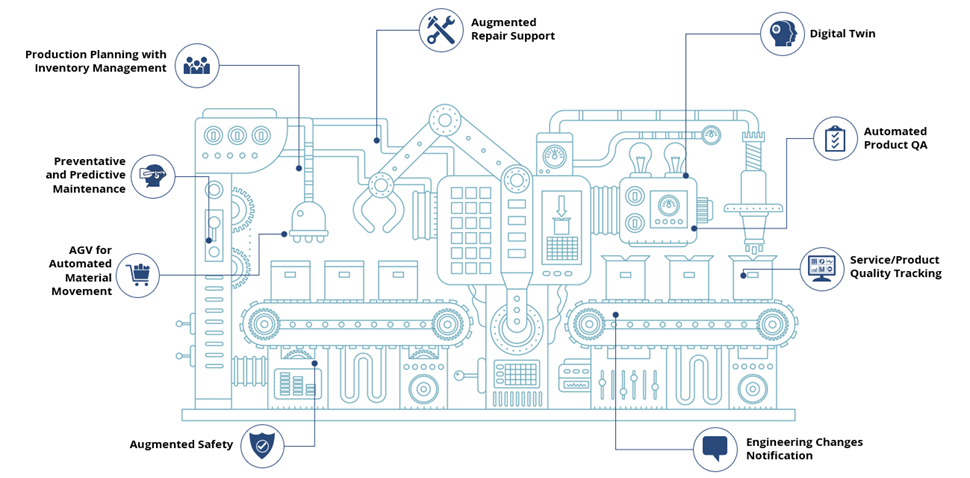
Figure 3: Factory of the Future
The trend that brought this to the fore was that consumers were no longer purchasing products in isolation. They expected to use their products in an extended service ecosystem tailored to experiences that suit their needs and lifestyles. One example is electric vehicles. These drivers need access to frictionless infotainment and seamless charging services, both of which come from players in the ecosystem other than the original equipment manufacturer (OEM).
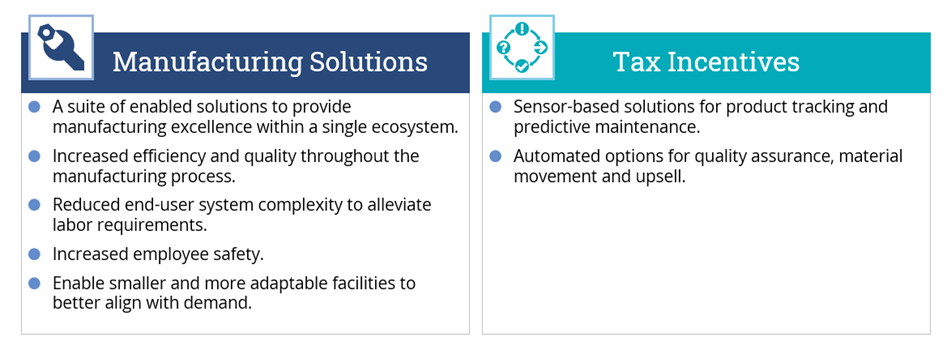
Figure 4: IT-OT Convergence Impacts Manufacturing Solutions and Taxes
IT-OT convergence not only enables such services for the customer but also delivers never-before-available value across the supply chain.
While technology is essential to convergence, a fallacy exists regarding what convergence truly entails. Convergence is not the same thing for all implementations, and it most certainly is not to be confused with technology alone. IT-OT convergence should occur based on the needs of the manufacturer, including processes, platforms and physical elements. The below diagram provides some of the use cases and applications of convergence in manufacturing.
Convergence Roadmap for Reliable Manufacturing Plants

Figure 5: Convergence Roadmap for Reliable and Predictable Manufacturing Plants
One important application of convergence is the need to satisfy increasingly stringent regulations for sustainability reporting. This goes beyond carbon emissions reporting to Scope III, which requires IT-OT integration to provide a manufacturer with a picture of usage. Regulations such as the Corporate Sustainability Due Diligence Directive (CSDDD) in the EU will require organizations to report on social factors such as engagement and reparation for impacted communities (a big factor in the location of extraction of raw materials). This will not be possible without extractable data and the right processes in place.
What Are the Challenges to Convergence?
Convergence even in theory is a demanding topic. We have already discussed the differences between OT and IT in architecture, approach and human talent.
Many OT traditionalists strongly oppose convergence at the device communication and integration level because of these complexities. For example, the duplicated naming conventions of programmable logic controller (PLC) systems would cause immediate conflicts on the network, collisions of information and confusion to existing address protocols and conventions.
Due to the typical age and physical isolation of OT systems, they are prime environments for security breaches. They would need to be remediated before they are made available for wider connectivity, even within a manufacturing plant or shop floor.
While data that exists in IT and OT systems are in high demand, accessing it requires overcoming challenges. The capacity of data produced in OT systems far exceeds what IT systems have been able to handle. The answer is not necessarily to create more data centers or quantum computers, as these are rather unsustainable solutions. And first understanding the data and its potential is often difficult. Engineers on the shop floor and in the manufacturing plant may not be aware of advanced data analytics techniques, and data scientists in IT may not be familiar with the domain expertise in manufacturing, which could result in spurious analysis.
Advocacy and sponsorship of an IT-OT convergence program can not lie in IT or OT alone. However, selecting a single individual or group to take on the convergence initiative is also not simple. Questions will arise about whose investment, budget and regions should be prioritized.
IT-OT Convergence Requires an Ecosystem with Many Players
At this point, OEMs may be concerned about where to start or which system to integrate first. Not all forms of convergence are required. Instead, OEMs should focus on partnerships they can rely on to build and support their convergence journey.
Mature manufacturers should know their value proposition and be clear on their core expertise, where they want to invest and which future projects to begin building. Some enterprises have made direct acquisitions to provide extensible functionality and others have developed relationships to co-create new services and products. According to the ISG Smart Manufacturing Survey, 70% of manufacturers agree that their ecosystems will change significantly.
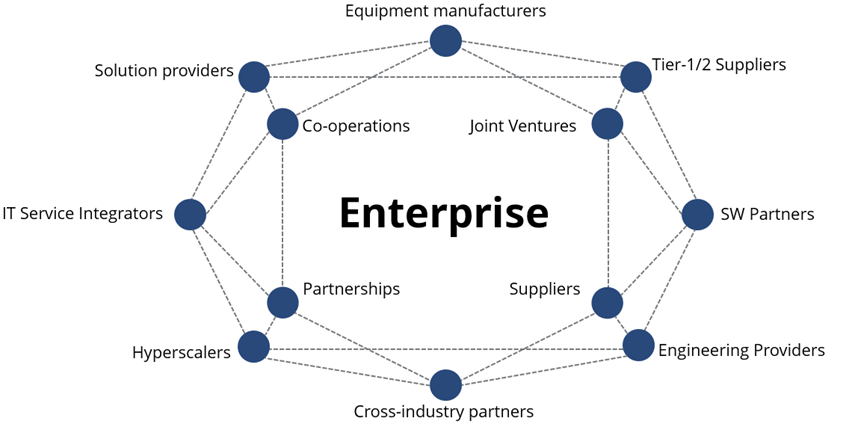
Figure 6: Connected Manufacturing Ecosystem
A True Story of a Manufacturing IT-OT Convergence Journey
An ISG manufacturing client sought guidance on how to achieve high-value outcomes from sales and growth in the aftermarket, new product-and-part sales and reductions in warranty costs. Key to solving this was understanding the clients’ customers and its entire value chain to identify opportunities for providing solutions. We advised a plan that included weaving together specific capabilities across the value chain into a digital thread that went beyond technology and included key people, process, data and platforms to achieve business outcomes.
One of these threads was focused on tracking parts and manufacturing components. Up to 20% of components had not been tracked, and the missing information was impacting reuse, warranty and customer retention. By helping the client find the right partners to form a digital thread across data, platforms and processes, we initiated an IT-OT convergence.
The conversation did not start with technology but with the definition of the problem statement, outcomes and business value. Once this was identified, the client could prioritize high-value opportunities (e.g., location, plant), resources (e.g., cost, people, products), efficiency (e.g., time), and sales and aftersales. This ultimately led to a solution architecture and high-level roadmap to optimize the enterprise’s convergence and ongoing capabilities.
How to Approach the Convergence Journey
Enterprises can facilitate the convergence journey with the following steps:
- Understand the organization and define its mission, vision, goals and aspirations.
- Understand the behavior, buying habits and usage of your product with your end customers across the value chain.
- Revisit the product strategy.
- Develop the business architecture.
- Solve foundational technical challenges (60% of enterprises say they are still dealing with these).
- Define the future profile of talent and their working patterns; engage your top talent to co-create this with you.
- Create a funding investment plan.
- Integrate the functional silos.
- Build with your partner ecosystem.
How ISG Can Help You
ISG helps manufacturers navigate the changing technology market and leverage digital technologies to support their future business goals. Contact us to find out how we can help.