Nearly 95% of decision-makers interviewed in our most recent ISG Digital Sustainability Study told us their external mission statement includes some kind of sustainability goal. We found companies are supporting these commitments by spending one out of every $500 on sustainability technologies. Today, we’re seeing that most of this spending is going toward compliance and reporting solutions rather than on digital programs that drive actual business benefits. And while 74% of the enterprises we interviewed have set net-zero emissions decarbonization targets, only 20% are consistently meeting them.
How should enterprises address gaps between sustainability goals and execution?
Sustainability is an important consideration in all industries today, but manufacturers are under even more pressure to adopt sustainable practices due to their use of physical resources and their by products. Manufacturing enterprises are using four key principles as a framework for sustainability solutions: reduce, reuse, recycle and recover. We’ll share example use cases of each of these principles below.
Sustainability Investments that Drive Product and Service Adoption
A best practice we are seeing is when companies embed a sustainability initiative – and related goals of decarbonization and achieving net-zero status – into their organizational culture, innovation framework, governance structures, reporting systems and overall mission. Rather than viewing it solely as an initiative that raises operating costs, these companies see sustainability as an investment that creates value and delivers better outcomes in both the short and long term. For instance, cement manufacturer LafargeHolcim is merging sustainability and innovation into a single C-suite role.
When ISG asked our top manufacturing clients about their plans to incorporate sustainability across the design and manufacturing value chain, 50% said their companies have set sustainability targets as key performance indicators and are making investments to meet the targets.
Source: ISG Digital Engineering and Manufacturing Transformation Survey 2023
Tackling Scope 3 Supply Chain Emissions
Our research also found that 85% of enterprises have engaged managed services providers in relation to their environmental, social and governance (ESG) goals, whether directly on an ESG project or woven into existing engagements or partnerships. Companies prefer to engage with providers that demonstrate a strong commitment to supply chain sustainability, so they can position themselves as leaders in this domain. They seek strategic collaborations with partners that possess the appropriate technological expertise. Regardless of company size, prevalent practices include supplier audits, supply chain mapping and adherence to codes of conduct.
To mitigate the risk of supply chain emissions, manufacturers are investing in energy-efficient technologies within their facilities. Some are also embracing renewable energy sources, diminishing reliance on fossil fuels and reducing emissions. Transportation and logistics present an opportunity for companies to minimize emissions with fuel-efficient or electric vehicles and streamline delivery routes. By embracing circular economy models, as mentioned above, manufacturers and their providers can reduce waste and extend product lifecycles by recycling, reusing materials and designing products for easier disassembly.Please fill out this form to continue.
Innovating with Digital Technology to Increase Sustainability
Reporting sustainability is a large consideration for many companies. When ISG asked our top manufacturing clients about their use of technology to monitor, track and report sustainability, 40% said they have dedicated systems to manage the reporting of sustainability performance. However, another 40% stated they manually gather data in bespoke spreadsheets.
How Companies Are Using Technology to Monitor, Track and Report Sustainability Efforts
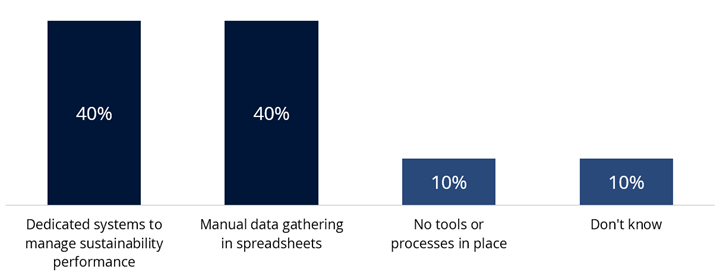
Source: ISG Digital Engineering and Manufacturing Transformation Survey 2023
Growth through Sustainability in Manufacturing
Global manufacturing companies, especially publicly traded organizations, have been incorporating environmental, social and governance (ESG) programs into their business operations for many decades. And, due to mounting pressures from employees, customers, community leaders and regulatory agencies, there is growing momentum for increasing and accelerating the pace of these programs.
A major driver is the investor community, which is asking companies to set aggressive ESG goals, measure progress against benchmarks and report accordingly. Based on a U.S. Sustainable Investment Forum (SIF) Foundation report, U.S. assets under management using ESG strategies increased by 42% from $12 trillion to $17 trillion between 2018 and 2020. Bloomberg Intelligence estimates that ESG assets under management may reach $53 trillion by 2025.
While each component of ESG is vital, the environmental aspect is especially relevant to global manufacturing companies. The World Economic Forum (WEF) has identified seven environmental themes across current ESG reporting standards. These themes are foundational for manufacturers: climate change, nature loss, freshwater availability, air pollution, water pollution, solid waste and resource availability.
Regulatory agencies are pressuring manufacturers to up their game. For example, a European Union regulation is requiring manufacturers to cut carbon emissions by at least 55% by 2030. The U.S. has pledged to reduce carbon emissions by 50-52% in the same timeframe.
Direct and indirect greenhouse gas emissions (GHG emissions) are a critical part of many company’s ESG goals. Many of the largest industrial, automotive, aerospace and heavy-duty manufacturing organizations report on their GHG emissions mitigation plans, carbon footprint reduction targets and emission metrics. Consider any product manufacturer, from food and beverage to consumer electronics to fashion clothing, they all have published corporate sustainability reports.
Increasingly, manufacturers are expected to embrace a dual mission of profitability and sustainability. Efforts to mitigate each of the seven WEF environmental themes are at the top of manufacturing companies’ agendas. Discrete manufacturing companies have been and are well positioned to understand, manage and mitigate their environmental impact thanks to their collective progress in digitizing operations and supply chains.
Smart Manufacturing Initiatives
Manufacturing companies have been steadily adopting Internet of Things (IoT) technologies. Sensors have been in plant floor operations for over 50 years; however, the need to connect them and leverage the data across multiple disciplines has increased dramatically over the last decade. This has propelled a similar rise in big data and analytics to gain insights in operations, optimize processes and make rapid decisions.
Robotics and automation have been the calling card for improved productivity in manufacturing since the 1960s, and some would argue even earlier. Driven by demand for increased efficiency, precision and flexibility across industries, there are over 3.4 million industrial robots in use around the world today. The global robot-to-human ratio in the manufacturing industry is 1 to 71, and some project revenue in the robotics industry to hit $43.3 billion by 2027.
Digital twin adoption has gained traction, especially for simulation, prototyping and process optimization. This has largely been driven by recognized benefits in faster product lifecycle development, production efficiencies and operational performance improvements.
Artificial intelligence (AI) and machine learning (ML) have been dominating the news cycle recently, and it has been welcome news for manufacturing companies leveraging its capabilities in predictive maintenance, quality control and supply chain optimization. As AI continues to advance, the consensus is that it will transform virtually all aspects of the manufacturing process.
Optimizing the Production Environment with Manufacturing Technology
Many manufacturers across the various sub-verticals, including discrete, process, make-to-order and small-batch companies, have adopted smart manufacturing practices to enhance sustainability and energy efficiency and align with corporate environmental goals. A leading global consultancy reported over 72% of manufacturers had sustainability as a key initiative in their business strategy.
Some examples of ways companies are using technology to improve sustainability include:
- Energy management systems that use software and hardware to monitor, control and optimize energy consumption. This allows real-time adjustments to energy usage, pin-points energy-intensive spikes and processes and enables proactive measures to reduce energy consumption.
- Renewable energy integration continues to gain momentum as improvements in solar panels and wind turbine technologies have been integrated with some of the smart manufacturing practices listed above. These technologies combine with other practices to reduce a company’s overall carbon footprint to support sustainability goals.
Taking Action: Steps to Start on Your Sustainability Roadmap
For manufacturing companies, the adoption of ESG goals is not just good for the environment, social and governance benefits. It has now become an imperative for strategic advantage, talent acquisition and retention, brand awareness and profitability. Like all strategic initiatives, companies looking to achieve their goals, increase their adoption and get out in front of the curve need to establish a roadmap. ISG recommends taking these steps and considerations:
- Set stretch goals for ESG and communicate them constantly along with your progress to all your stakeholders.
- Connect every aspect of measurement to focus on customer and employee experience.
- Integrate various smart manufacturing and new technologies throughout your supply chain; make supply chain integration an area of broad emphasis.
- Include organizational change management at the forefront and as a foundation throughout your roadmap.
- It’s a journey, play the long game.
Frequently asked questions:
How are sustainability and ESG related?
ESG stands for environmental, social and governance. Sustainability is a component of ESG relating most closely to the environmental aspect with connections also to social and governance in terms of organizational culture and regulation, respectively.
How are manufacturers putting reduce, reuse, recycle and recover into practice?
- Reduce: Manufacturers are actively addressing carbon emissions by transforming raw materials into products while concurrently minimizing waste. Technology is key here. New tools help manufacturers analyze real-time data on energy consumption, waste generation and other environmental metrics. For example, Tesla has been leveraging six years of sensor data from its Gigafactory Nevada to train an artificial intelligence (AI) program to safely control 195 interconnected HVAC units, accounting for 6MW of total electrical load. AI is expected to provide significant energy savings for Tesla as it scales to control a larger proportion of HVAC equipment at Gigafactory Nevada and HVAC equipment at the company's other factories.
- Reuse: Companies are avoiding hazardous or virgin materials for production processes. For example, Caterpillar’s energy conservation projects at its San Luis Potosi, Mexico, facility is using 100% on-site renewable solar electricity. In total, the site has been able to reduce its overall energy consumption by more than 35% from a 2018 baseline.
- Recycle: Companies like Boeing are transforming manufacturing processes to create products with fewer materials, facilitating disassembly for reuse of functional parts. Boeing's design strategies allow for parts and materials recovery, making their airplanes nearly 90% recyclable by weight. By employing additive manufacturing technologies like 3D printing to achieve this, they are reducing raw material usage, minimizing waste and enhancing fuel efficiency.
- Recover: Companies are recovering waste materials to generate energy. For example, Unilever is in partnership with LafargeHolcim and its waste management service provider Geocycle to pre-treat waste materials to use as alternative fuel. Even the ash byproduct is fully incorporated into the cement mixer, leaving no residues. Additionally, the company continues to recover value from unavoidable waste streams by extracting a renewable fuel called biogas to fuel some of its thermal heating output – an innovative solution to aid its decarbonization program.
Acknowledgement
This paper benefited from the contribution of Kathy Rudy, Chief Data and Analytics Officer, ISG.